Amazing Cordillerans Slideshow: Benedict’s trip to Baguio City (near Baguio) was created with TripAdvisor TripWow!
The Intertech logo is a representation of people, their development, our concern for the environment.
Nickel-Laden road beds
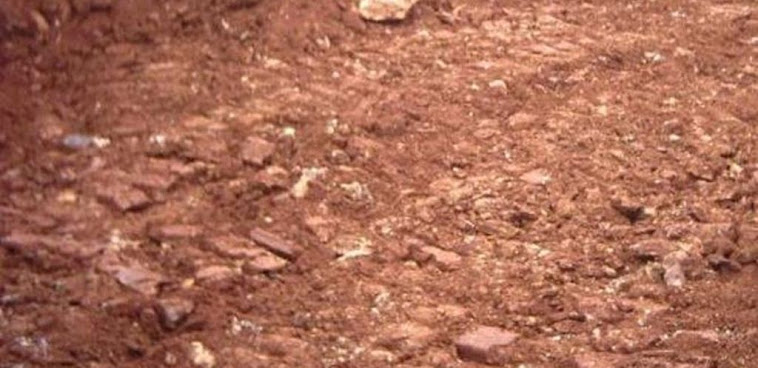
A cooperative mining project - in a reality of people, their struggles and their loves . .
Thursday, October 4, 2012
Friday, September 28, 2012
Chairperson Macrina Santela of MARU BAGAC FOUNDATION & Bene Ballug of Maru- President of FEM
Approved corporate structure and composition
+ expenses
Mga etiketa:
kubos,
maru bagac,
maru offices,
maru-FEM
Mga etiketa:
Ballug,
bene,
Intertech President
Sunday, September 23, 2012
Monday, September 10, 2012
The Family that supported our on-going project at Zambales and "agri-development" at Floridablanca, Pampanga Phils.-
Ballug Family and Major Bong and Iza Gaces
with the Project Leader- Bene Ilacad Ballug
Thursday, August 9, 2012
Happy birthday to Pheith Iena on August 12rth - I love you sweetheart -
and Happy birthday to Pherst on the 21st both august month-
and i dedicate this month-long celebration to my kids- whom i love so much-
GOD has blessed me with their lives and thank GOD for them. - from DAD
How can a green building consultant, architect, engineer or builder get a market advantage in today’s constrained economy, when everyone has lots of green building experience, dozens if not hundreds of LEED APs, capabilities and experience in each market sector? I will tell you: One way to stand out is to become an advocate for “disruptive” approaches, ways of approaching sustainable design, green building, and green product development that advance the state of the art, while at the same time improve performance and cut costs.
The idea of “disruptive technologies” or “disruptive innovations” was first posited by Professor Clayton Christiansen of Harvard Business School 15 years ago, in The Innovator’s Dilemma. It is used to describe innovations that create new markets and value networks, and eventually go on to disrupt existing markets and value networks (over a few years or sometimes decades), displacing earlier technologies. Over time, what may have been initially an inferior (but cheaper) solution gives rise to a continuous wave of innovation that displaces a formerly superior technology or business model. Think of what the iPod did to reinvent and save the recording industry.
What does this have to do with green building? I will argue that, over the past dozen years since LEED came onto the scene, green building has NOT fundamentally changed how the business of building design, construction and operations works. In fact, the rapid adoption of green building techniques and systems by existing organizations in the building industry has not changed the relative strength of any of the companies involved in design, construction and building operations. And there have been, in fact, no new entrants of consequence into the industry, beyond a few materials suppliers.
But clients keep looking for better solutions. If you look at the relatively high ratio of dissatisfied to satisfied clients, it would be extremely upsetting for the architecture/engineering/construction (A/E/C) industry. It’s very much a case, as my mother used to say, of better the devil you know than the devil you don’t. Buildings still don’t work very well when built and most building operators still struggle to keep up with the modest technological innovations in green building, such as better building controls, radiant heating and cooling, etc. What clients really want is the ability to make a quantum leap in performance at lower cost. Where will they find those attributes? More importantly, how can your organization find, develop and deliver such disruptive innovations?
This past week, I received a newsletter from the managing principal of a mid-sized architectural firm that lamented the lack of disruptive thinking in the architectural business. He mentioned recently attending a technology conference hosted by Wired magazine, at which he was the only architect. By contrast, he noted, the most recent conference of the American Institute of Architects contained nothing really new, with a program designed mostly for architects to get their annual quota of continuing education hours.
It got me thinking: where should the US green building industry (and, by extension, all architecture, engineering, construction, commissioning and building operations firms) be looking for new ideas? Here are a few suggestions:
Geographic expansion: My own experience is that we are rapid adopters of other people’s ideas, such as new design approaches from Europe, including underfloor air distribution, double-skin façades, radiant heating/cooling, wood technology and climate engineering, to mention a few. So, the obvious thing to do is to send your cleverest people to Europe for six weeks on “voyages of discovery” to learn what’s new and report back to the rest. Or, perhaps better yet, go to China and find out how entire hotels are being built in 30 days. Perhaps study every industry that’s building $50-$100 million products to see what you can learn. This might include ship building, commercial aviation, etc. Who’s going to be sent on the next trip to Europe or China, the firm’s current leaders or the smartest “up and comers”?
Industry technology transfer: What about looking seriously at Lean manufacturing as a way to reinvent design and construction practices? Lean manufacturing has been well studied and practiced for more than 20 years. Hire a lean manufacturing “sensei” for your firm to re-engineer all your design practices, don’t just adopt BIM or Revit and call it a day. This may mean an entirely different hiring paradigm for most firms, where industrial engineering is more highly valued than education and experience mechanical engineering or architecture, for example. Can you widen the job descriptions and qualifications for your openings to attract more “interesting and qualified” people?
By Paul Hawken- USA
Monday, July 23, 2012
Friday, July 13, 2012
Wednesday, July 11, 2012
Sunday, June 17, 2012
Friday, June 15, 2012
March 27th : Sumitomo eyes New Caledonia, Philippines for nickel…………March 27th : Authorities seize 15 water pumps………….March 27th : Gold Fields hints at buying a 100% stake in Philippine project…………March 27th : Rationalization of requirements, processes for new power ventures urged.
MARCH 27, 2012 BY ADMIN
March 27th : Sumitomo eyes New Caledonia, Philippines for nickel.
TOKYO (Reuters) – Sumitomo Metal Mining Co (5713.T) is looking to increase nickel supplies from New Caledonia, the Philippines and the Solomon Islands to make up for a shortage expected to hit Japan once Indonesia bans unprocessed nickel exports from 2014.
Japan gets more than half its nickel supply from Indonesia and its top two ferro-nickel producers, Sumitomo Metal Mining and unlisted Pacific Metals Co, are expected to take a major hit from Indonesia’s new 2014 export law.
“We are talking with the Indonesian government if it’s possible to export what it cannot process at home,” Nobu Kemori, president of Sumitomo Metal Mining, told Reuters in an interview.
“We believe that possibility is not low given a lack of smelter capacity in Indonesia, costs and time involved in building new smelters, including facilities such as power plants. But at the same time we are looking to increase supply from New Caledonia, the Philippines and the Solomons.”
Indonesia has said it will ban shipments of some unprocessed metals – copper, gold, tin, nickel, among others – from 2014 to improve domestic metal production capacity, boost supplies of refined products to the domestic market and increase government revenue.
Indonesia’s ban on exports could lead to a scramble by global consumers for minerals from elsewhere, with the shrinking supply outlook ultimately supporting benchmark prices.
Kemori said the firm’s 62.5 percent-owned Taganito nickel project in the Philippines will start production in July or August 2013, with output in 2014 seen reaching at least 27,000 metric tonnes (29,762 tons), or 90 percent of its capacity.
An attack by Maoist rebels late last year has pushed back the launch of the project valued at more than $1 billion by a couple of months and raised the cost by some $100 million, he said.
In 2010, Japan imported 40,000 metric tonnes (44,092 tons) of nickel from Indonesia out of a total of 77,000 metric tonnes (84,878 tons), according to customs-cleared statistics.
Indonesia, home to the world’s largest copper and gold mine, accounted for 20 percent of Japan’s total copper imports of 1.3 million metric tonnes (1.43 million tons) in 2010.
Sumitomo Mining, Japan’s No. 2 copper smelter, is boosting investment in upstream assets of copper, nickel and gold to raise its self-sufficiency in these raw materials, with a view that an increase in demand from emerging markets will outstrip supply, particularly in copper.
“A slowdown of the Chinese economy is a concern, but its huge supply shortage of copper, estimated at 2.6 million tonnes a year, won’t vanish soon,” he said.
Sumitomo now sells about half of its about 400,000 metric tonnes (440,925 tons) copper cathode output in overseas markets, he said.
By Yuko Inoue and Yuka Obayashi, Reuters.
——————————————————————————————————————————————————
March 27th : Authorities seize 15 water pumps.
OPERATIVES from Opol Municipal Police Station and the Regional Public Safety Battalion (RPSB) confiscated 15 water pumps and 30 meters hose used for hydraulic mining during a joint operation along Iponan River last week.
Misamis Oriental Vice Governor Norris C. Babiera, co-chair of the Provincial Peace and Order Council (PPOC), said the joint operation was conducted along Iponan River particularly on the riverside of Barangays Cauyonan, Nangcaon, Tingalan and Bagocboc in Opol town.
Babiera said no one was arrested during the operation.
“The machines were left by operators prior to the operation,” he said.
Though no one was arrested, Babiera expressed his gratitude to the unified members of Task Force Iponan along with the Opol Municipal Police Station, RPSB, Philippine National Police, Philippine Public Safety College (PPSC), Mines and Geosciences Bureau, Archdiocese of Cagayan de Oro, Armed Forces of the Philippines particularly the Philippine Air Force and Philippine Army, non-government organizations and the Cagayan de Oro City Police Office.
At least 10 personnel from Opol Police Station led by Police Senior Inspector Rogelio Labor along with 36 RPSB-PNP personnel led by Police Inspector Edcel Caramonte and 10 personnel from PPSC led by Police Inspector Sebastian Chua joined the operation.
By Michael Andrew W. Yu, Sun Star, Cagayan de Oro.
——————————————————————————————————————————————————-
March 27th : Gold Fields hints at buying a 100% stake in Philippine project.
The miner has the option to acquire 100% of the Guinaoang porphyry copper-gold deposit in the Philippines after it exercised an option last week to take a 40% stake in another project, Far Southeast.
Gold Fields, the world’s fourth-largest bullion producer, said on Monday it was looking to acquire a 100 percent stake in a second gold-copper project in the Philippines as it continues to diversify from its home base.
“We have an option to acquire 100 percent of the Guinaoang deposit for a payment of $63 million and that option exists up until early next year,” Gold Fields Chief Executive Nick Holland told the Reuters Global Mining and Metals Summit.
Gold Fields last week exercised an option to take a 40 percent stake in another project, Far Southeast, in the country after making a $110 million down payment. It retained the option to acquire an additional 20 percent in the project.
Guinaoang lies about 4 kilometres (2-1/2 miles) from the Far Southeast Project and has a similar style of mineralisation.
The option agreement was concluded with Bezant Resources to acquire the entire issued share capital of subsidiary company Asean Copper Investments, which in turn holds the Guinaoang porphyry copper-gold deposit.
Holland has also not ruled out buying out its joint venture partner in the Far Southeast Project.
“If the opportunity arose in these kind of assets, clearly it is something we would look at,” he said during the summit at Reuters’ Johannesburg office.
“Whether or not we would be able to take a bigger stake in Far Southeast depends on the view of our joint venture, Lepanto Mining. At this stage they seem to be very happy with their participation in the project,” Holland said.
Last year Gold Fields spent $1 billion on acquiring the minority interests in mines it already owned and operated. This saw it take 100 percent ownership of its mines in Peru and Ghana.
Holland added that he thought the Far Southeast Project would be “very comparable” to the promising Wafi-Golpu project being developed by Harmony Gold Mining and Newcrest Mining in Papua New Guinea.
Author: By Sherilee Lakmidas, Reuters.
——————————————————————————————————————————————————–
March 27th : Rationalization of requirements, processes for new power ventures urged.
GENERAL SANTOS CITY — The national government will need to rationalize the current requirements and processes for ventures on power generation facilities if it wants to resolve the ongoing power shortage in Mindanao in a shorter period, an official of a local electric cooperative said.
Engr. Santiago Tudio, general manager of South Cotabato I Electric Cooperative (Socoteco I), said a number of companies had signified to invest on new power generation plants or facilities in Mindanao but most of them later withdrew supposedly due to the stringent requirements set by the government over such projects.
“The problem is that, an investor will need to get 111 government permits and clearances for every power plant that they will put up and the processing of all these requirements usually take about two years,” he said.
As a result, Tudio said power investment experts estimated that it would take three to four years for a power plant project to become fully operational.
He cited the case of the 200-megawatt (MW) coal-fired power plant of the Alcantara-led Conal Holdings Corp. in Barangay Kamanga, Maasim town in Sarangani that was slated to become fully operational by the year 2014.
The construction of the US$ 450-million power plant, which will be operated by Conal’s subsidiary Sarangani Energy Corp., formally started in November last year.
“The processes should be cut down to more reasonable level so more investors or companies will be encouraged to invest in power generation,” he said in a radio interview.
Tudio was among the local electric cooperative executives from Mindanao who recently met with Energy Secretary Jose Rene Almendras in Manila to discuss various pressing concerns of the island’s power sector.
He said they tackled possible solutions to the worsening power supply deficit in Mindanao that already triggered extended daily rotating brownouts.
During their meeting, Tudio said Almendras reiterated that the government prefers the utilization of coal energy to ease Mindanao’s power supply shortage, which is pegged at an average of 142.5 MW based on estimates made by the National Grid Corp. of the Philippines (NGCP).
According to the NGCP’s power supply outlook for this week, Mindanao’s power generation capacity stands at 1,142 MW while the peak demand was estimated at an average of 1,284.5 MW.
The deficit, which was reportedly caused by the dwindling capacity of the National Power Corporation’s hydroelectric plants, has so far triggered daily rotational brownouts extending to about 12 hours in several parts of Mindanao.
In Socoteco I’s service area, which comprises Koronadal City and eight neighboring municipalities in South Cotabato and Sultan Kudarat provinces, it implements daily power curtailments of one to two hours.
In this city, Socoteco II implements two-hour daily curtailments but officials said the situation may worsen in the coming weeks due to the unstable condition of NPC’s power plants.
“There’s no immediate solution to this problem right now and I think we have to contend with it until the Maasim coal plant becomes operational in two years,” Tudio said.
Aside from the Maasim plant, he said they are also pinning their hopes on AboitizPower Corporation’s 200 MW coal plant in Davao City that was also targeted to become operational by 2014.
He added that San Miguel Corp. (SMC) is also finalizing the plans for its proposed 150 MW coal-fired power plant in this city.
SMC has been building up its presence in nearby South Cotabato province following its earlier acquisition of a major coal mining project in Barangay Ned in Lake Sebu town.
Sultan Energy Philippines Corp. sold its coal mine project in Lake Sebu in June 2010 to SMC, which also holds the coal operating contract of Daguma Agro Minerals Inc. in the same area.
Studies said the coal mining area, which is part of the mineral-rich Daguma Mountain Range, contains 426 million metric tons of coal deposits.
Initial exploration and drilling results have blocked 55 million metric tons of reserves that can be mined in 526 hectares of the mountain range.
Tudio said SMC was bent on pursuing their coal plant project despite earlier findings that the area’s coal deposits were not yet mature or fully developed.
“But they (SMC) will reportedly be putting up a plant that were designed to process the type of coal deposits found in Lake Sebu,” he added.(PNA).
By Zambotimes.
Monday, June 4, 2012
Model Master development - Phase 2
Model Retirees Homes

Paper Processing facility for Kenaf
Wednesday, May 30, 2012
Sunday, May 27, 2012
Farm Edge Planning
Tuesday, May 1, 2012
A SALUTE TO OUR WORKERS IN THE PHILIPPINES AND OUR OFWs WORLD-WIDE- MAY YOUR INCREASES IN SALARIES BE GRANTED- WE AT INTERTECH MAY SOON ADOPT A METHODICAL SALARY SCHEME THAT PROMOTES EXCELENCE IN THE WORK PLACE- WHERE SUCCESS ARE GIVEN PO-RATED CASH BONUSES ASIDE FROM A COMPETETIVE SALARY SCHEME FOR ITS WORK FORCE-
WE LOVE YOU AS OUR OWN. .
FROM MANAGEMENT
Saturday, April 28, 2012
INTERTECH SHALL HELP MARU BAGAC IN THE PROJECT CONCEPTUALIZATION, DEVELOPMENT AND FINANCING OF
THE SO-CALLED "MARU BAGAC FOOD VALLEY - AGRI ECONOMIC ZONE" TO BE PROPOSED TO GOVERNMENT.
Friday, April 27, 2012
Tuesday, April 24, 2012
KENAF PROJECT (BALLBROS & MARU BAGAC)
Kenaf is a 4,000 year old NEW crop with roots in ancient Africa. A member of the hibiscus family (Hibiscus cannabinus L), it is related to cotton and okra. It offers a way to make paper without cutting trees. Kenaf grows quickly, rising to heights of 12-14 feet in as little as 4 to 5 months.
While the flowering can last 3 to 4 weeks, or more, per plant, each individual flower blooms for only one day. The stalk of the kenaf plant consists of two distinct fiber types.
The outer fiber is called “bast” and comprises roughly 40% of the stalk’s dry weight. The refined bast fibers measure 2.6mm and are similar to the best softwood fibers used to make paper.
The whiter, inner fiber is called “core”, and comprises 60% of the stalk’s dry weight. These refined fibers measure .6mm and are comparable to hardwood tree fibers, which are used in a widening range of paper products.
The Philippines spends a considerable amount of foreign exchange for fiber imports. From 1984 to 1986, the government spent US $404,282 or about P9 million to buy 1,117,783 kg of kenaf fibers needed in making gunny sacks.
To reduce the country’s expenses, and eventually to stop importing fibers and start earning from it, the Fiber Development Authority (FIDA) is urging farmers to plant kenaf.
Kenaf (Hibiscus cannabinus Linn.) is an annual bast fiber plant believed to come from the subtropical regions of Asia and Africa, and brought to the country by Dr. Nemesio Mendiola in August, 1927 from Buiterzong, Java.
Most kenaf plants have spiny petioles, stems and calyx. These spines cause severe itchiness when they come in contact with the skin.
Kenaf grows from 1.83 to 3.7 m high with a diameter of 12 mm. Its ornamental flowers are clean-colored in the morning and gradually turn to pink in the afternoon.
Kenaf fiber is used for fishing nets, ropes and doormats while woven fabric can be made into carpets, cloth and clothes lining.
The most important use of kenaf is in sack making. While the threat of synthetics replacing natural fiber is present, the latter ads qualities which synthetics cannot match.
For one, natural fiber is twice as durable- and more reusable- as synthetic sacks. The former is also able to store grains longer without damaging their eating and milling quality.
Moreover, synthetic sacks cannot be piled up to 18 feet while natural sacks can be piled twice higher. And this is important since millers want their warehouses fully packed.
Today kenaf is being developed for other uses. Researchers have found that its leaves are used as food in Ghana and as livestock feed in the U.S.A. The Bureau of Plant Industry has discovered that the leaves are a very good medium of mushroom spawns due to their 24 per cent crude protein content.
Its wood, however, shows the most promise as a potential source of pulp and paper. Kenaf may also be used as a blending agent to improve lower quality pulps. Tests show that kenaf pulps perform equally well as most softwood and are superior to most hardwood pulps. Moreover, handsheets and experimental papers from them have good bursting quality, tensile strength, folding endurance, surface finish, printing and writing qualities.
There are many kenaf varieties planted in the Philippines. Traditional varieties used are Viridia Vulgaris, Cuban, Everglades, Guatemala, Manchurian, Giza and Java jute, all of which are spiny. Among them, Cuba 108 and G-2 yield the most fibers.
At present , Kenaf varieties are mostly spineless. Thanks to Dr. Nemesio Mendiola and Francisco Cabato Jr. who, in 1965, produced spineless kenaf varieties A59-80, NSDB-63-1 and NSDB-63- 11.
Kenaf grows well in a variety of soil but it does best in deep, rich loam that is neither acidic nor alkaline.
To ensure a good crop, soil must have sufficient amount of organic matter. It must be well-drained even if the plant can stand short periods of shallow standing water. Marginal kenaf also be planted on if the fertilizer is applied.
Kenaf needs a tropical to subtropical climate. It prefers an elevation below 3,000 feet and a rainfall of 25-35 inches during its growing period. Ideal places are those with even rainfall distribution since continuous rain cause yellowing of the leaves. They should also have no marked dry and wet seasons and be far from the typhoon belt. Typhoons can easily fell the plant due to its height and weak root system.
Kenaf plants are photoperiodic; they are sensitive to sunlight. Based on their needed sunlight, kenaf are classified into: long-day, short-day and day-neutral plants.
Long-day plants require 12 hours of sunlight to reach the following stage. Short-day plants need less than 12 hours while day-neutral are not affected by the length of exposure and, hence, can be planted any time of the year.
Since kenaf is photoperiodic, the time of planting is important. For fiber production, plant kenaf during the months of April to October to expose the plant to long daylight. It requires 12-1/2 to 12-3/4 hours or longer to produce long stems of 15 feet or more. To produce seeds, plant kenaf from November to December when daylight is short.
In planting kenaf, plow the land once or twice depending on the soil type. Make furrows 12 to 24 inches apart for fiber and seed production, respectively.
If the soil is moist, seeds sprout in about 5 days or earlier. When the seedlings are a foot high, thin them until only 2 inches separate each seedling. Thinning can fill up vacant hills.
The most important operation during the plant’s early life are weeding and occasional tillage. Weeding is done 3 to 4 weeks after planting. Once the plants are established and have outgrown the weeds, these operations are no longer needed.
Two hundred to 250 kg of ammonium sulfate with 21 per cent nitrogen give better yields. Apply this on the furrows and cover with soil 2-3 cm thick before sowing. Apply fertilizer again 18-25 days after sowing when the seeds have sprouted. Apply again when the plants are 60-70 days old around the area 4 cm from the plant’s base, then cover with soil.
Kenaf plants are prone to small black fly beetle and tussock moth. Fly beetle attacks the plant’s leaves and stems at its latter stage of growth. Control this pest by harvesting early infested areas or by spraying with contact insecticide. The tussock moth, on the other hand, bore holes on the stem.
Anthracnose, leaf-mosaic, petiole-curls and root nematode are the common disease plaguing the kenaf plant.
A fungal disease, anthracnose infects young leaves, stipules and meristems or growing tips which turn brown, wither and die. When the entire plant afflicted, only the withered stems remains. Control this by spraying copper oxychloride on the leaves every other week. Before planting on previously affected areas, treat them with 50 kg potassium per hectare.
Leaf mosaic causes a chlorotic mottling of leaf lamina resulting in low yield. Spray infected area with kersoap pesticide. To prevent this disease, thoroughly analyze the soil and apply balanced nutrients before planting.
A viral disease that causes extreme curling and twisting of the particles is petiole curls. Soil deficiency causes this hence, soil analysis is necessary. Prevent this from spreading: pick out curled leaves burn them. Kersoap pesticide may also be sprayed.
The worst disease of kenaf is the “bohon” causing root nematode which stunts growth, causes yellow foliage and even death. Nodular galls also appear at the roots. To control it, overflood the area nematodes alternately with kenaf. Applying pesticides like Biocon is another way of controlling this disease.
Harvest kenaf by cutting the stem near the plant’s base with a sharp bolo or any cutting tool. Bundle the stem at a diameter of 20 cm. Leave them in the field until the leaves drop; this can serve as mulch for the soil.
In one harvest, average yield of a hectare is 2,000 kg of dry fiber. For spineless varieties, a hectare may yield 70 -80 tons of green stalks or 3,000-4,000 kg representing four to five per cent fiber recovery.
The best time to harvest kenaf for fiber is during the plant’s flowering stage of about months after planting when fiber quality and quantity are at its highest. This also lessens the plant’s exposure to pest, disease and unfavorable weather condition which results in lower yield and profit.
If fiber is harvested before flowering, fiber yield is lower; and if done after its quality is poor.
Harvesting kenaf for seeds, on the other hand, is done 4 to 5 1/2 months after planting when 80 per cent of the plants have 5 to 6 dried capsules. Generally, yield of seeds from 1 to 2 hectares is sufficient to plant 100 hectares.
There are three ways of extracting fiber from the plant’s stalks: using machines, retting or applying chemicals.
Decorticating machines used for abaca, ramie and sisal hemp can be use to extract kenaf fiber. First, cut the stalk close to the ground, defolaite, bundle and haul them to the stripping sheds and to the machines. Soak fibers in water in several days, wash and dry in the sun.
In retting, bacteria or fungi act on the gummy substances where the fibers are imbedded. The bundles of stalks are immersed in a meter-deep water for 10-16 days, or in a sea water for 12 days until the fibers cling loosely to the stalk’s pith and thus, can be easily separated.
Retting period depends upon the plant’s age, water temperature, its circulation, mineral, bacteria and fungi content. To hasten this process, keep water temperature at 32o- 36oC and add hay or straw to feed the bacteria or fungi especially if the water is clean.
Using chemicals in extracting fibers is performed under controlled conditions. Remove the bark by ribboning and treat with chemical. Here is one of the formulas: for every 400 lb of ribbons, use 400 gallons of water, 40-60 lb of ordinary soap and 7 lb of ammonium sulfate. Maintain temperature of the mixture at 60o-65oC for one hour and stir it constantly.
the standard grades of kenaf depends on its strength, type go cleaning and color. There are four standard grades of kenaf wither retted or decorticated:
KR-1 or kenaf excellent. The fiber is soft, silky, fine and free of gummy scales and ever-retted fibers. The color is dull white and the cleaning is excellent.
KR-2 or kenaf Good. The fiber is medium soft with little, thin gummy scales. The color is dingy white and the cleaning is good.
KR-3 or Kenaf Fair. The fiber contains many scales and some bark due to the bruised stems. The color is dingy light brown and the texture is harsh while cleaning is generally fair.
KR-X or Kenaf Mixed. The fibers has not been thoroughly washed and there are many gummy scales with pith clinging to the fibers which stick together especially towards the butt. The color ranges from dull to dark brown.
Dried Kenaf fiber is prepared to shipping or storage by baling. The standard bales has a net weight of 125 kg measuring 100 by 55 x 60 cm. Bales can be stored for many months in a dry, relatively dark warehouse.
Other Uses of Kenaf
End-use products depend on the fiber portion used. Bast fiber goes to make such products as burlap, carpet padding, and pulp. The short-fibered core is processed into poultry house bedding, packing material, oil-absorbent mats, and other items.
Another market for kenaf is in pulp for the newsprint industry. Kenaf-based newsprint is strong (and thus well adapted to modern newsprint machinery), has good ink retention, and does not yellow with age as readily as wood-pulp-based newsprint. Of course kenaf fiber must compete directly with wood pulp prices, since both are used to produce newsprint.
Kenaf can also be used for bean stakes, animal litter, a fiberglass substitute in molded plastic, a fiber source for improving recycled paper quality, a bulking agent for composting sewage sludge, a cellulose fiber for composition panels and boards, and a potting-mix ingredient.
Kenaf also makes excellent animal forage. The crude protein levels in kenaf leaves range from 15 to 35 percent. Kenaf harvested as livestock feed should be cut 75 to 100 days after planting to gain optimum protein production per acre. Generally, after 80 days of growth, fibers build up in the stem, the leaf-to-stem ratio changes, and the protein level drops.
source: region10.dost.gov.ph, visionpaper.com, attra.ncat.org, photo from bfafh.de, doa.go.th
For more information, contact:
Dept. of Science and Technology
Rm. 303 DOST Bldg., DOST Complex,
Gen. Santos Ave., Bicutan, Taguig City 1631
Telephone Nos: (632) 837-20-71 to 82
Fax: (632) 837-8937
Web: www.dost.gov.ph
Dept.of Agriculture
D.A. Compound, Elliptical Rd.,
Diliman,Quezon City
Tel. Nos. (632) 929-6065 to 67 / 920-3991 / 928-1134
Web: www.da.gov.ph
Share
Read Related Posts:
Mga etiketa:
kenaf processing,
kenaf production
Sunday, April 15, 2012
INTERTECH UPDATES
INTERTECH
SAN FERNANDO, PAMPANGA
6 POTENTIAL BUYERS FROM PAKISTAN, CHINA, JAPAN, SINGAPORE, AUSTRALIA - HAVE SENT THEIR CORPORATE INQUIRIES REGARDING INTERTECHS PRODUCTION OF NICKEL AND CHROMITE- ASKING FOR DIRECT SUPPLY CONTRACTS.
WE SHALL BE RESPONDING TO THEM UPON THE COMPLETION OF OUR PRODUCTION PREPARATIONS THAT HAVE STARTED AFTER HOLY WEEK OF APRIL THSI YEAR 2012.
WE SHALL LIKEWISE BE SENDING THE BOARD OF DIRECTORS CORRESPONDING DATA SHEETS REGARDING THE SPECIFICS OF THE INQUIRIES TO BUY ORES FROM INTERTECH FROM THE VARIOUS NAMED END-USERS AND AGENTS ..
BENE BALLUG
President
Tuesday, March 27, 2012
Share Maru Bagac Foundation slide show
Maru Bagac Foundation Farm Slideshow: Benedict’s trip from Luzon, Philippines to Angeles City (near Angeles) was created by TripAdvisor. See another Angeles slideshow. Take your travel photos and make a slideshow for free.
Sapang Bato Farms
Mga etiketa:
food valley,
foundation. agri zone
Subscribe to:
Posts (Atom)